Electrical Transformer: Working Principle, Construction, and Types
Understanding Electrical Transformers: Definition, Working Principle and Construction
An electrical transformer is a static electromagnetic device designed to transfer alternating current (A.C.) energy from a primary circuit to a secondary circuit while maintaining the same frequency. This transformation modifies the voltage and current to meet specific requirements in power transmission and distribution.
A transformer's core, typically made from cold-rolled grain-oriented (C.R.G.O.) steel sheets, is engineered to minimize energy losses and optimize magnetic flux. The device consists of two or more windings:
- Primary winding: Receives the input A.C. energy.
- Secondary winding: Delivers the transformed energy.
In an auto-transformer, the windings are both electromagnetically and electrically coupled.
Transformers are classified based on their windings and applications:
- A transformer with two windings is called a double-wound transformer.
- A transformer with three or more windings is known as a multi-winding transformer.
By design, transformers are further categorized into:
- Single-phase transformers: Suitable for residential or small-scale applications.
- Three-phase transformers: Common in industrial and commercial power systems.
- Polyphase transformers: Feature interconnected windings to deliver consistent voltage in multi-phase systems.
The windings are also classified by voltage:
- High-voltage (H.V.) winding: Connected to the circuit with higher voltage.
- Low-voltage (L.V.) winding: Connected to the circuit with lower voltage.
Depending on the voltage transformation:
- A step-down transformer decreases voltage.
- A step-up transformer increases the voltage.
Some transformers are equipped with taps on their windings to adjust the voltage or current ratio, making them versatile for various applications.
For insulation and cooling, transformers are often immersed in transformer oil within a sealed tank. These are referred to as oil-immersed transformers. In contrast, dry transformers use air or other materials for insulation and are ideal for environments where liquid insulation isn’t practical.
Working Principle of a Transformer
A transformer is a static electrical device designed to transfer power from one circuit to another without altering the frequency. It operates by increasing or decreasing voltage levels while inversely adjusting current levels. This functionality is essential for efficient power transmission across electrical systems.
The principle of operation is based on mutual inductance: when an alternating current (A.C.) flows through the primary winding, it creates a magnetic field that induces voltage in the secondary winding. The primary winding receives the electrical input, and the secondary winding delivers the output.
Both windings are made from insulated copper or aluminum and are wound on a laminated core made of magnetic material. This core reduces energy losses and enhances the magnetic flux necessary for efficient energy transfer.
 |
Fig.2.1 Magnetic circuit and windings of Transformer |
The basis of the evolution of a transformer is the formation of mutual inductance between two coils sharing the same magnetic flux through a path of low reluctance as shown in Fig. 2.1.
The mutual inductance is extremely high between these two coils inside a transformer. If one coil is connected to a source of alternating voltage, an alternating flux gets formed within the laminated core, most of which is linked up with the secondary side, inside which the formation of mutually induced emf ( Electromotive force) takes place. The equation for Faraday's laws of electromagnetic induction, i.e.

If the second circuit is closed, a current flows in it, so the electric energy is transferred from the primary one to the secondary one.
Understanding Transformer Ratings: Key Specifications and Measurements
A transformer has several important rated quantities, such as power, voltage, and frequency, which are typically specified on the manufacturer’s nameplate. These ratings provide essential information for understanding the transformer's capabilities and proper use. In addition to these, other rated quantities—such as efficiency and temperature conditions of the cooling medium—are also important but might not be explicitly listed on the nameplate.
Here are the key transformer ratings:
Rated Duty: The rated duty of a transformer is determined by the quantities provided on the nameplate, indicating its design limits for operation.
Rated Power: The rated power of a transformer is the output power at the secondary terminals, usually expressed in KVA (kilovolt-amperes). This is the maximum power the transformer can supply without overloading.
Rated Primary Voltage: This is the voltage indicated on the nameplate for the primary winding. If the transformer has taps on the primary, the rated tapped voltage will be specifically noted.
Rated Secondary Voltage: The secondary voltage is the voltage across the transformer’s secondary terminals when there is no load, and the primary side is operating at its rated voltage. If the secondary winding has taps, the rated voltages for each tap will be clearly specified.
Rated Current: The rated primary and secondary currents are calculated based on the rated power and voltage values provided on the nameplate. These indicate the maximum safe current levels for the transformer.
Kinds of transformers
The transformers mentioned in the list are the most important ones:
1. Power Transformers are used for the transmission and distribution of electric power over long distances.
2. Autotransformers are used for converting voltages within relatively small limits to connect power systems of different voltages to start A.C. Motors etc.
5. Power transformers can also be used for special applications like furnace and welding etc.
Transformer construction
All the transformers have the following essential elements
1. All the transformers except auto-transformers can have more than two windings insulated from each other and the core.
2. A core which in the case of a single-phase distribution transformers usually comprises a cold-rolled Silicon Steel strip instead of an assembly of punched Silicon Steel laminations such as are used in the larger power transformer cores. The flux flows parallelly to the direction of steel's grain or 'orientation' inside the core. This results in a reduction in core losses for a given flux density and frequency, or it allows the use of higher core densities by keeping the size of transformers small against different core losses.
Other necessary parts are:
1. A suitable container for the assembled core and windings.
2. A suitable medium for insulating the core and its windings from each other and from the container.
3. suitable bushings for insulating and bringing the terminals of the windings out of the case.
A transformer has two basic types of construction :
1. core type transformer.
2 shell-type transformers.
Both the type of transformer has a different arrangement of copper conductors and iron core. Core type transformers have an iron core visually surrounded by copper but in the shell-type transformers, the iron surrounds the copper winding.
Core type transformer
The complete magnetic circuit of the core-type transformer is in the shape of the hollow rectangle exactly as shown in fig.2. in which Io is the no-load current and fi is the flux produced by it. N1 and N2 are the numbers of turns on the primary and secondary sides respectively.
 |
Fig.2. The magnetic circuit of a core-type transformer |
The core is made up of silicon-Steel laminations which are either rectangular or
L-shaped with the coils wound on two legs, the appearance is that of fig.3. if the two coils shown here, are the respective high and low side coils as shown in fig.3, the leakage reactance would be much too great. In order to provide maximum linkage between windings, the group on each leg is made up of both high-tension and low-tension coils. This may be seen in fig.4, where a cross-sectional cut is taken across the legs of the core. By placing the high-voltage winding around the low voltage winding, only one layer of High-Voltage insulation is required, that between the two coils. If the high-voltage coils were adjacent to the core, an additional high-Voltage insulation layer would be necessary between the coils and the iron core.
 |
Fig.3&4 cross-section of a core-type transformer |
Fig.5 shows the coils and laminations of a core-type transformer with a cruciform Core and circular coils.
 |
Fig.5.coils and laminations of a core-type transformer |
Rectangular cores as shown in Fig.6a with rectangular cylindrical coils can be used for small-size core-type transformers. For large-size transformers, it becomes wasteful to use for rectangular cylindrical coils and so circular cylindrical coils are preferred. For such purposes 'square cores may be used as shown in fig.6b where circles represent the tubular former carrying the coils. Evidently, a considerable amount of useful space is still wasted. A common improvement on the square core is to employ a 'cruciform core', which is shown in fig.6c which demands, at least, two sizes of core strips. For very large transformers, further core stepping is done as shown in fig.6 where at least three sizes of core plates are necessary. Core stepping not only gives a high space factor but also results in reduced length of the mean turn and the consequent I2R loss. The three-stepped core is the most commonly used although more steps may be used for very large transformers as shown in fig.6e.
Shell type transformer
one can see in fig.7 that the shell-type transformer has the Iron fully surrounding the copper. E-shaped and F-shaped laminations are stacked together to form a core that looks like numeric eight.
 |
Fig.6. various types of transformer cores |
Fig.6 shows the different types of cores used in core type transformers.
 |
Fig.7. shell-type transformer |
The Centre leg has all the windings placed on it. A high-side coil arrangement is made adjacent to the low-side coil to reduce the leakage flux. Both the windows are fully occupied by the coils, which are flat or pancake in shape, and most of the time it is made up of copper strips. A low voltage coil arrangement is made adjacent to the iron core to keep the usage of high voltage insulation low.
Choice of core or shell-type construction
Core type transformers consists of a core with a higher mean length and lower coil turn. Core type transformers have a small cross-section of iron, and so to increase the flux, a higher no of turns of wire will be required across the core. Core type transformers can be better utilized at places where high voltage is required. Shell type core can manage the coil's high mechanical stress or forces exerted radially, better than core type at the time of dangerous short-circuits.
 |
Fig.8.coils and laminations of a shell-type transformer |
Core type and shell-type cores have similar characteristics but vary in cost.
Voltage rating, KVA rating, weight, insulation stress, mechanical stress, and heat distribution are the factors that can differentiate the choice for the two types of core.
Spiral core Transformer
One can see the spiral core in fig.9. The core is formed with a long thin strip of CRGO(cold rolled grain oriented) steel sheet wound in the shape of a circular or elliptical cylinder. The core can also be constructed with a group of short strips laminated with each other to form an elliptical type core.
 |
Fig.9.spiral-core transformer |
Such kind of core construction is always useful to achieve the desired flow of flux along with the 'orientation' or the grain of the iron used in assembling the core. It becomes possible for a transformer to operate at higher flux density with a reduced loss per kg and less weight per KVA with the help of cold-rolled steel of high silicon content.
Transformer windings, Terminals, Tappings, and bushings
Transformer windings
The most important requirements of transformer windings are:
1. The construction cost of winding should be cost-effective in both the cases such as the availability of copper in the market and the maintenance-free working of the transformer for a longer period.
2. The heating of the winding should not be in access to the minimum standard requirements. Neglecting overheating against the standard requirement will bring down the service life of the transformer.
3. The winding should have proper mechanical support against the forces exerted on it during a sudden short circuit.
4. The winding should have the necessary electrical strength with respect to overvoltages.
Different types of windings are classified and briefly discussed below:
1. Concentric winding types are cross-over, helical, and disc.
1. Concentric windings are used in core-type transformers where each limb is wound with many other coils including both primary and secondary turns that can also be concentric cylinders.
1. Concentric windings as shown in fig.10. These winding are used for core-type transformers. Each limb is wound with many coils in a group containing both primary and secondary turns which may also look like concentric cylinders. The placement of L.V. winding is done just next to the core and that of H.V. winding outside the core. In order to reduce leakage reactance, the two windings get subdivided and are tightly fixed with high tension and low tension section differently. These windings can be further divided as follows:
 |
Fig.10.Concentric coils |
1. Cross-over windings:-Cross-over windings can sustain currents up to 20A. Hence these are used in the H.V. winding of small transformers. The round wire type conductor comes with the covering of cotton and strip-type conductors come with the covering of paper. Initially, Cross-over coils are fixed and wound over the formers. Each coil is constructed with many no of layers and each layer comes with a different number of turns. Each winding is constructed with many layers connected in series. Both ends of the coil are brought out from inside and outside of the coil. The inside end of a coil is connected with the outside end of the other coil placed next to it.
2. Helical winding:-The construction of helical winding is done with the help of rectangular strips wound in the shape of a helix. The arrangement of copper strips is such that they are wound in parallel radially. Here the total no turns of the coil occupies the total radial section of winding. Helical coils are mostly used in the construction of L.V. windings of large transformers. With additional insulation between layers apart from the insulation of conductors, these can also be used in the construction of H.V windings for large transformers.
3. Continuous disc winding:- The construction of this kind of winding takes place with the help of a number of flat copper strip wound spirally from inside radially outwards. The thin strip of a copper conductor is used in sufficient length, needed for complete winding or section of winding between tappings. The copper conductor with a single strip or a number of strips put in parallel is also used in the construction of this winding. This kind of winding formation takes place with the help of the robust construction of each disc. The discs are wound on insulating cylinders. These cylinders are separated from the discs with the help of thin strips sticked along the length of the cylinder. The discs are insulated from each other with the help of pressboard sectors attached to the vertical strips. The vertical and horizontal space provide ducts for free circulation of oil which is in contact with every turn.
2. Sandwich coils:- Sandwich coils as shown in fig.11 are employed in transformers of shell type. Both high and low-voltage windings are split into a number of sections. The formation of this winding is in such a way that each High Voltage section lies in between the low-voltage sections. It is possible to achieve the desired leakage reactance by the way of division of windings inside the sandwich coils.
 |
Fig.11.sandwich coils |
Terminals and leads:- The windings are connected with insulated copper rods or bars. The Leads should be free from bends and corners to avoid corona and dielectric loss in High Voltage transformers. Winding Connections in air-cooled transformers are taken to the busbar while in the case of oil-cooled Transformers, winding connections are taken to the insulated bushings.
Tappings:- The voltage in the supply network is controlled by changing the transformation ratio. It is achieved by tapping the winding and changing the number of turns. The change in the number of turns may be affected when the transformer is out of the circuit known as off load tap changing or when onload known as on load tap changing. The tappings are provided on the high voltage winding because a fine voltage variation is obtained to a large number of turns. It is difficult to obtain voltage variation within closed percentage limits in low voltage winding as there are few turns and voltage per turn is a large percentage of the total voltage.
In transformers, the tappings can be provided at:
1. Phase ends
2. Neutral point or in the middle of the windings.
The advantage of providing tappings at phase ends is that the number of bushing insulators is reduced, this is important where the cover space is limited. Some transformers have reinforced insulation at the phase ends. It is essential that in such cases either the taping should not be provided at the end turns or the reinforcement should be carried beyond the lower tap.
At the time of construction of tappings at the neutral point, the insulation between various parts is kept small. This kind of arrangement is very cost effective in the case of High Voltage transformers.
Bushings:-The terminals of the winding are brought out of the tank to connect with the bushings and then the bushings are connected to the external circuit. The porcelain bushings are connected with the conductor at the point of entry at the top of the tank in low voltage transformers. Large size bushings are used in high voltage transformers. Large porcelain or composition bushings are used for 33kv type transformers, above that Oil Filled or condenser type bushings are used.
Transformer cooling methods
For dry-type transformers up to 25KVA, cooling methods are:-
1. Air natural:- The natural surrounding air is used in this method to cool the heat generated by losses.The winding enclosed by a sheet metal protects the winding from mechanical injury.
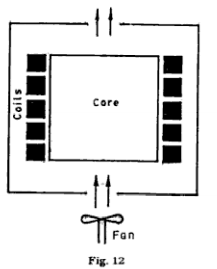 |
Fig.12. Air blast transformer |
2. Air blast:-In this method, the transformer is cooled by a continuous blast of cool air circulated through the core and winding shown in fig.12. The blast is created by a fan attached outside to the transformer. The air supply must be dust-free to prevent the accumulation of dust in ventilating ducts.
Oil Immersed Transformers uses mineral oil for cooling and these are classified as:
1. Oil-immersed self-cooled transformers
The inside part of the transformer is immersed in oil and heat is generated in cores and windings is passed to the oil by conduction. The hot oil in contact with the core and winding rises and is displaced by cool oil from the bottom. The hot natural oil slowly transfers its heat to the tank walls from where heat is taken away by the ambient air. The oil gets cooler and falls to the bottom from where it is dissipated into the surroundings.
 |
Fig.13 Transformer with cooling tubes |
For large voltage rating transformers, the tank surface should be plain and large enough for proper heat dissipation with the help of auxiliary means like fans, etc. As both space and oil are costly, these auxiliary means should not increase the cubic capacity of the tank. The heat-dissipating capacity can be increased by providing corrugations, fins, tubes shown in Fig.13. and radiator tanks. The advantage of 'oil natural cooling is that it does not clog the ducts and the windings are free from the effects of moisture.
2. Oil-immersed forced air-cooled transformers:- This type of cooling is achieved, with the help of cool air directed over the outer surfaces of the tank of the transformer immersed in oil.
3. Oil-immersed water-cooled transformers:- Here the oil is cooled by pumping the cool water through the metallic coil immersed in the oil just below the top of the tank. Thereafter, the hot water is cooled in a spray pond or a cooling tower.
4. Oil-immersed forced oil-cooled transformers:- Here the oil is cooled by pumping it upward and downward to the winding with the help of radiators and in turn, the radiators are cooled by the way of external fans. The cooling of transformers having capacities from 10000 KVA and higher are shown in fig14. In such cases, airblast cooling of the radiator is used.
 |
Fig.14.Air blast cooling of radiator |
Transformer oil
It is a mineral oil obtained by refining crude petroleum. It serves the following purposes:
1. Provides additional insulation
2. carries away the heat generated in the core and coils
3. Protects the paper from dirt and moisture.
The transformer oil should possess the following properties:
1. High dielectric strength
2. low viscosity to provide good heat transfer.
3. Good resistance to the emulsion.
4. Free from inorganic acid, alkali, and corrosive sulphur.
5. Free from sledging under normal operating conditions.
6. High flash fire point.
Conservator:- The Transformer oil looses its insulating properties when it comes in contact with the surrounding natural air and attracts moisture hence it should be protected from coming in direct contact with the atmospheric air.
Also, air may cause acidity and sledging of oil. This is prevented by fixing the conservator over the top of the transformer tank. The function of a conservator as shown in fig.14 is to take up contraction and expansion of oil without allowing it to come in contact with outside air. The conservator has an airtight metal drum set above the level of the top of the tank and connected with it by a pipe. The main tank gets completely filled when the oil gets cold. The conservator is partially filled with oil. So the possibility of the oil surface coming in contact with air is greatly reduced. Here the sludge formed, sets in the conservator, and does not go up to the main tank.
Breather:- when the temperature changes the oil expands or contract and there is a displacement of air. During the cooling of the transformer, the air is drawn in and the oil level goes down. This is called breathing. When the air comes inside the transformer tank, it is passed through an external device called a breather for the purpose of extracting moisture. The breather has a small vessel that contains a drying agent like Silica Gel crystal impregnated with Cobalt crystal. This dry agent inside the breather helps its to filter the moisture from the air.
Sledging takes place when there is a slow formation of solid hydrocarbons due to the heating and oxidation process of the transformer oil. Slowly the sludge starts depositing itself on the windings and cooling ducts due to which the transformer gets overheated. The sledging formation is a continuous process, till the time, transformer remains hot.
Oxidation takes place when the oil comes in direct contact with air.
This comment has been removed by a blog administrator.
ReplyDeleteNice. Thanks for the great information. NEMR is known as one of the best 63kva Distribution Transformer. NEMR Industries provides reliable and efficient 63kva distribution transformer for smooth supply to varied uses. These transformers come with advanced features to assure stable voltage, minimize loss, and have no trouble even under tough conditions.
ReplyDelete